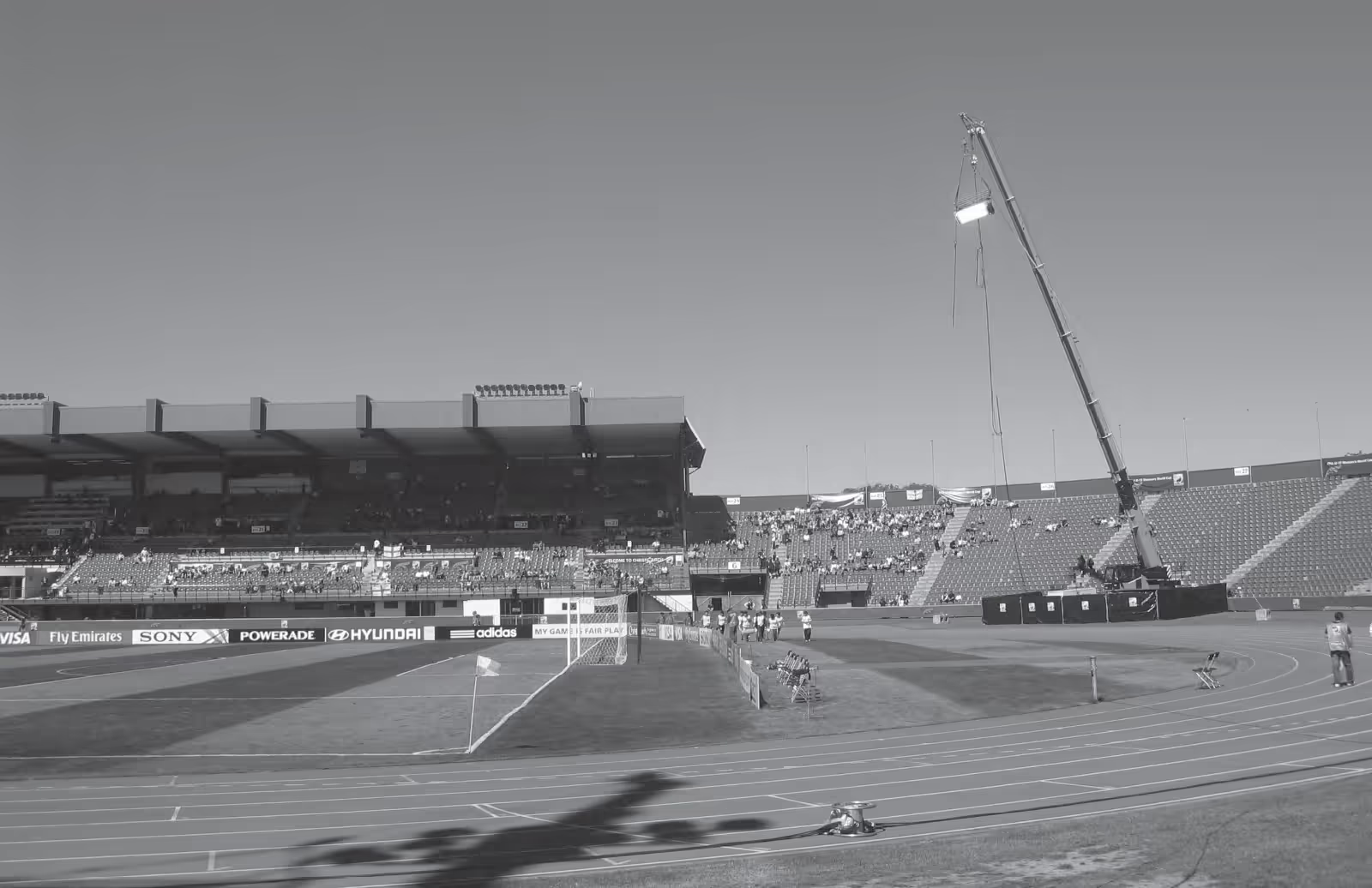
Lighting up in Christchurch
It all started with a phone call six months ago, as most of our jobs do – Don Meggatt from On Site Broadcasting in Christchurch. “Can you light a soccer pitch at night to TV spec?”
“Yes.”
“That wasn’t the reply I expected.”
“Well, it won’t be cheap, but we have the technology - if you have the budget.”
“Leave it with me,” was Don’s reply.
I thought that would be the last I would hear of this job. Pity, because it would be a good job with a good challenge and some seriously good kit to play with.
One week later I got a phone call from Mike Okey, a Project Manager with the Christchurch City Council. “I understand you have spoken to Don from OSB and that you can provide a temporary lighting solution for Queen Elizabeth II Stadium for the FIFA Under 17 Women’s Soccer.”
“Yes, if you have the budget, we can do it.”
Mike explained that they were doing a scoping exercise to see if it was worth putting a permanent lighting rig into the park, or whether it was better to do it on a temporary basis, albeit only for two nights. Would I put together a price for the temporary solution?
I agreed to do a rough budget price; then if they decided to proceed I would provide a formal quote for the job.
I already had a concept in my head of using four 100kW Softsun® fixtures from Luminys Systems, one in each corner of the pitch, to replicate the typical stadium lighting found in most grounds.
I did some calculations and decided that this would allow us to achieve 1000 to 1200 lux across the pitch, which would meet the typical TV lighting level requirements.
In the meantime Mike had sent me the FIFA 35-page document on their TV lighting requirements and a drawing of the pitch as it lay within the stadium at QEII. The FIFA spec required a base level of 1400 lux or a level of 1800 lux if super slo-mos were going to be used. I made a quick call to Don to find out what he actually needed.
He assured me that 1200lux was heaps for both the intended SD and HD coverage of the games. We decided to use a fifth fixture in the centre of the pitch directly behind the camera position, to not only give a bit more lift to this area directly to camera, but also to offer some redundancy in the case of fixture failure during the live transmission.
I remembered that I had seen some photos of Softsuns® used to light soccer in Norway, so I contacted David Pringle at Luminys and got some copies and details of what they had used.
The next step was to figure out how to get the fixtures to a position that would achieve the light levels, but also keep the sources out of the FIFA exclusion zones around the corners. The ideal would have been three 25-metre and two 35-metre Condors, but there were none available in the South Island, so we opted for hydraulic cranes. Mike contacted Titan Cranes in Christchurch and they proposed using five 25-tonne, 35-metre units which they had. Three would be positioned in the western carpark and be able to reach over the embankment to place the Softsun® at the correct height and distance from the pitch on the camera side. On the eastern side we had the grandstand, so the cranes had to be on the edge of the running track which surrounds the soccer pitch. These two cranes had to get the fixtures to 35 metres high to achieve the correct lighting angles and not provide lens flare for the ground level cameras.
I decided to use a single genset for each Softsun®, both for redundancy and to keep the cable runs short and simple. We planned to place a 250kVA genset alongside each crane to power its fixture.
The pictures were submitted along with the rough budget to the council for them to make a decision on which approach they would take. Mike and his team weighed up both proposals and after a few weeks he called to say that they were going with our temporary proposal, and asked me to prepare a formal quote.
Fortunately I had most of the costings done already, so after checking I hadn’t missed anything vital, a quote was submitted. Mike phoned to say that it was all go. Normally the council issued a 75-page contract for this type of capital works, but since it was only a temporary job, we could make do with a five-page version. I waited in trepidation for this document.
It made interesting reading – the requirement for extensive insurance cover, the compliance with Transit NZ’s traffic plans, and a solid Health & Safety compliance document. Fortunately the council was dealing with the traffic plan, because I couldn’t think where the traffic was going to be! We had the insurance in place, and with a couple of hours work our H&S policy had the hazard identifications added to it to deal with cranes and public. The paperwork was done.
A phone call was made to our colleagues at Panalux in Sydney to book the three Softsun®s that they had, to add to the two that now live with us in Auckland - we had our five fixtures sorted. The next task was to organise freight. We have a very good freight forwarder who organised a 20ft container from Sydney directly into Christchurch for the Panalux units. She also suggested that if we had the time, it would be cheapest to containerise the two units out of Auckland along with all the rigging kit, and ship via coastal vessel to Christchurch. Good for the carbon footprint! This was organised and gave us our two on-site storage areas at the same time.
Now all we had to do was wait for the dates to arrive - not a luxury you normally have in this business!
In the meantime, I made a flying visit to Christchurch to check out the site, meet the crane supplier and check out the gensets. Alan Low from Titan Cranes is a typically laconic South Islander and a very experienced crane man. He had looked at the site and recommended a couple of changes. We were going to get a 90-tonne 4-wheel drive all-terrain unit to get inside the stadium. When I saw this beast in the yard, I realised this was a very serious Tonka toy. This job was getting better by the minute!
We were also going to get a 95-tonne unit for the western side, just to give us a little more reach. Titan would also handle and supply all the rigging of the units, so the H&S issues there were also covered.
Mike Okey also let me know that he was moving on from the Council, and the project management was being handed over to his replacement, Ian Davidson. There was a new relationship to set up.
We were lighting two games one week apart. For the first game, the lighting was to be set up and tested on the day/night before and then left in place for the game.
For the second game the lighting would be set up on the morning of the game. Unfortunately, no one had communicated this to the FIFA organising people.
On the first set-up day we got the cranes and gensets into position and Softsun®s in the air by mid-afternoon. FIFA were concerned about us working while the players were practising, even though we were separated by hundreds of metres. Mid-afternoon was also the time that a marketing guru from FIFA spotted the Titan name on the crane jibs, and we were told that they would have to be covered because they were not paying sponsors – the whole stadium had to be “clean” of advertising. There was a couple of hours of tense discussion. One solution suggested by our laconic crane supplier was that we remove the cranes altogether, but this caused a slight flurry from FIFA!
After all the “argy bargy”, there was a time set aside the next morning to cover the offending logos and we got on with the job in hand. At 2030 hours it was finally dark enough to get around with a light meter and check that my calculations were accurate. Better than expected - I was getting 1500 lux in the centre of the pitch and no less than 1400 lux toward the edges and over the sidelines. We put the units away for the night on a balmy Christchurch spring evening.
The next day dawned with rain, supposedly to clear by midday, but with a southerly change in the afternoon. Those of you who know Christchurch know that a southerly change is not good, as this generally means high winds and a cold snap, not great when you are hanging big lamps off cranes 35 metres high.
We got the cranes rigged by mid-afternoon, but there had already been one southerly change with sleet and rain, so the crane operators were reluctant to put the fixtures up in the high winds that followed. We waited as long as we could and endured another southerly change before finally getting the fixtures in the air. By this time the air temperature was 8 degrees and there was snow on the Port Hills!
The lights were on for the second live game, and as the sun sank in the west during the game, the lights came into play to cover the whole pitch. The OSB vision operators were very happy with the result, and commented that the lighting was a half-stop brighter than Wellington’s Cake Tin.
The units were packed away that night, the cranes departed, and we left for Auckland the next morning, ready to return the following week.
Then the phone calls started from the FIFA officials. “The cranes have to move, they are in the back of shots, they are ugly, we can still see logos”, etc, etc. “We need all the lights rigged for practice on the Wednesday” and other similar demands. None of this was in the budget.
After a couple of days of back-and-forth discussions, and a bit of re-jigging of our work times, most of these issues were resolved and we were able to get on with the job of lighting the football. We had resolved to get one fixture up for the practice on Wednesday night. This kept the FIFA officials happy; we then got the rest of the fixtures in the air and running by 1100 hours on the Thursday, in plenty of time for the first game at 1600 hours.
The two games went off without a hitch from our point of view, and we were able to sit back and watch some very good football. It’s good to watch players who don’t have to indulge in histrionics play a good solid game!
All in all, it was a good outcome for the games played in Christchurch. We got to use some good technology, and we can now confidently say that we can light a football pitch for TV at night!
As usual in this industry, it starts out as one person’s idea and is then seen through to fruition by a strong team of people all working together.
Credits:
Lighting Director: Chris McKenzie
Softsun® Technician: Ron Greig
Electricians: Steve Renwick & Steve Walker
Lighting Equipment: PLS
Freight: Burnard International, Donna McErlane
Cranes: Titan Cranes Christchurch, Alan Low
Generators: Hirequip
Christchurch City Council: Mike Okey, Ian Davidson

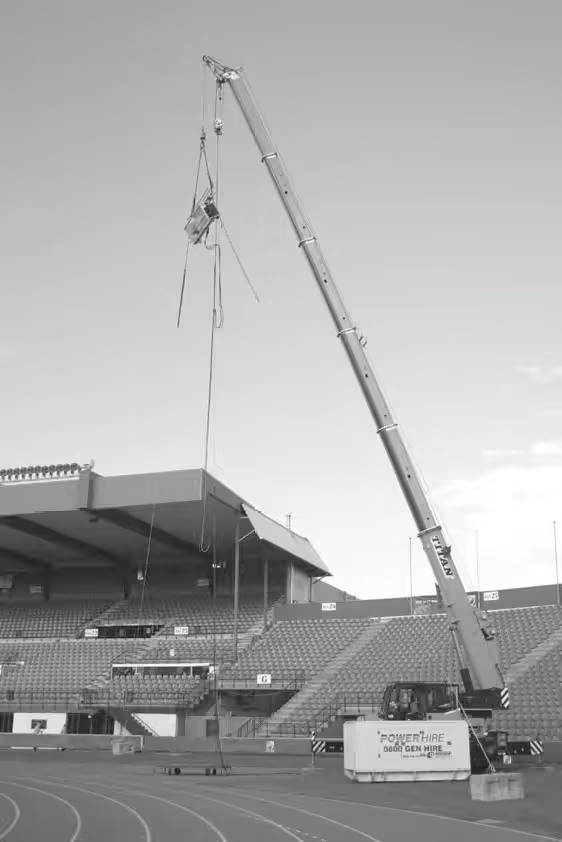
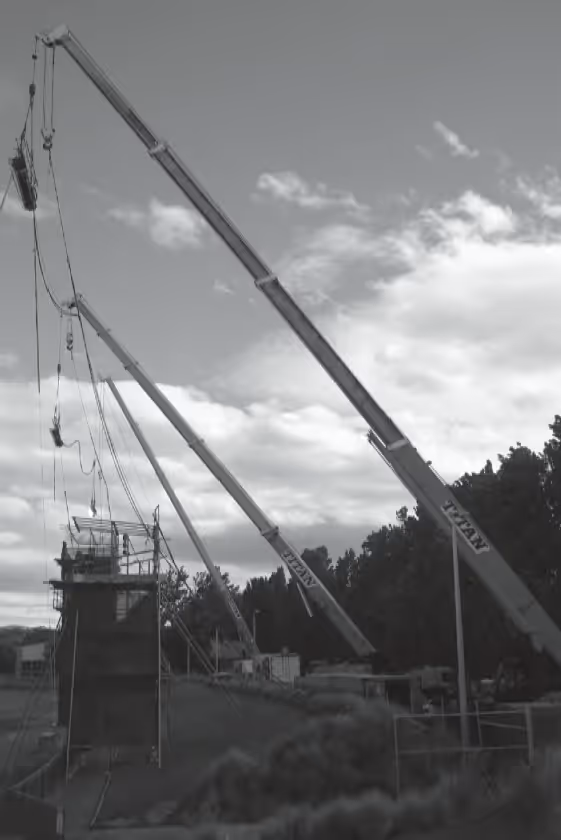
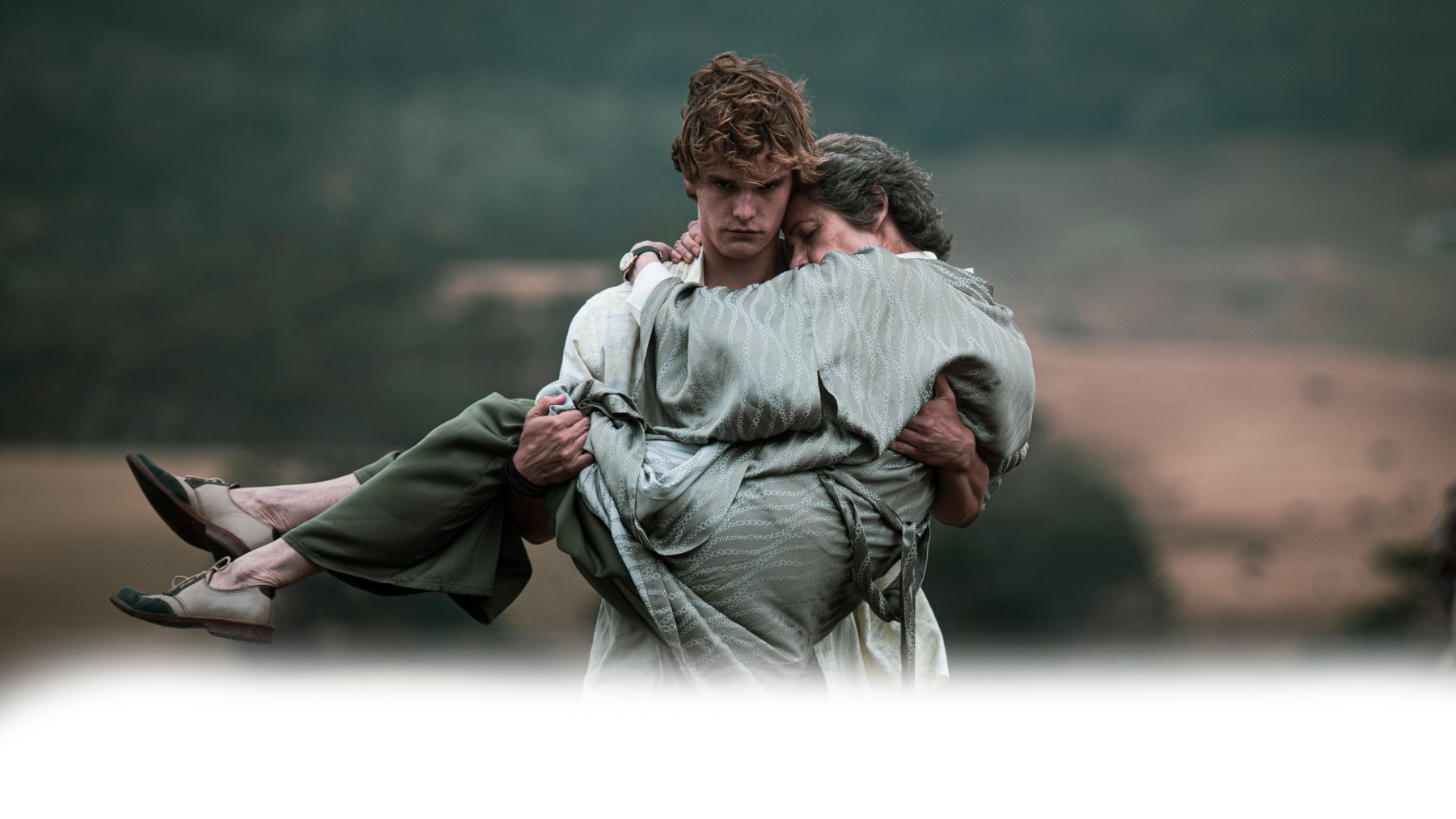